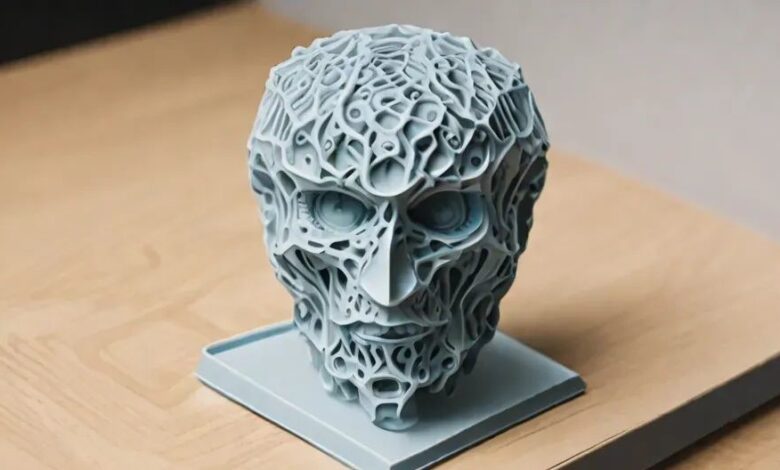
How to 3D Print – Top 7 Steps: Beginner’s Guide to Success
3D printing has become a transformative force in various industries, enabling the rapid production of prototypes and customized products.
This guide will outline seven essential steps to successfully navigate the world of 3D printing. Whether you’re a hobbyist or a budding entrepreneur, mastering these steps will help you utilize 3D printing technology effectively, ensuring high-quality results with your 3D printer.
What is 3D Printing and Why It’s Revolutionizing the World
3D printing, also known as additive manufacturing, is a revolutionary technology that creates a physical object by layering material based on a digital model. This process allows for the production of complex shapes and structures that traditional manufacturing methods cannot achieve. Its applications range from prototyping and healthcare to aerospace and automotive industries, making it a game-changer.
By using 3D printing, businesses can significantly reduce production times and costs, leading to increased efficiency. The ability to quickly create prototypes fosters innovation, allowing designers to test and iterate on their ideas more rapidly, which is essential in today’s fast-paced market.
The Basics of 3D Printing: An Overview for Beginners
At its core, 3D printing involves three main components: the 3D printer, the slicing software, and the 3D model. Beginners should start by understanding how these elements interact to produce a final product.
The 3D printer uses materials like thermoplastics, resin, or metals to create objects layer by layer. Slicing software, such as Cura, takes a digital model in STL format and converts it into instructions for the printer. This includes specifying details like layer height and infill density. With this foundational knowledge, beginners can explore the vast possibilities of 3D printing, from creating simple objects to more complex prototypes.
How 3D Printing is Transforming Industries: A Glimpse of Its Potential
3D printing technology is revolutionizing various industries by enabling rapid prototyping and customization. In the medical field, for example, 3D printing is used to create patient-specific implants and prosthetics, enhancing the quality of care. The aerospace and automotive sectors benefit from the ability to produce lightweight, intricate parts that improve performance and reduce material waste.
Additionally, the rise of decentralized manufacturing through 3D printing allows businesses to produce parts on-demand, reducing the need for large inventories. As industries continue to adopt this technology, it is clear that 3D printing will play a pivotal role in shaping the future of manufacturing and design.
Step 1: Choose the Right 3D Printer for Your Needs
Different Types of 3D Printers: FDM, SLA, and SLS – What’s Best for You?
When selecting a 3D printer, understanding the different types available is crucial. Fused Deposition Modeling (FDM) printers are popular for their affordability and ease of use, making them ideal for beginners. Stereolithography (SLA) printers, on the other hand, offer higher precision and smoother finishes, suitable for detailed models.
Selective Laser Sintering (SLS) printers are best for creating durable and complex parts using powdered materials. Each technology has its strengths and weaknesses, so it’s essential to consider what you intend to create and your budget. Evaluating your specific needs will help you choose the right 3D printer that aligns with your projects.
Key Features to Consider When Buying a 3D Printer
When purchasing a 3D printer, several key features should be considered to ensure it meets your requirements. Look for a printer’s build volume, which dictates the maximum size of the printed parts. Additionally, pay attention to the nozzle size and layer resolution, as these factors influence the print quality. Some printers come equipped with dual extruders, allowing for multi-material printing, which can enhance creativity.
Automated bed leveling and a heated print bed can also greatly improve print quality by ensuring better adhesion and reducing common printing problems. By assessing these features, you can make an informed decision that suits your 3D printing ambitions.
Step 2: Create or Download a 3D Model to Print
How to Design Your Own 3D Model Using CAD Software
Creating your own 3D model is an exciting way to personalize your 3D printing experience. Computer-Aided Design (CAD) software allows users to design intricate 3D objects tailored to their specifications.
Many software options, like Tinkercad and Fusion 360, offer user-friendly interfaces for beginners. When designing a 3D model, remember to consider the printer’s limitations, such as overhangs and minimum wall thickness. It’s important to ensure your design can be printed without issues, which may involve incorporating supports or selecting appropriate layer heights. By learning the basics of CAD, you can unleash your creativity and produce unique designs for your projects.
Where to Find Free and Paid 3D Models
If designing from scratch isn’t your preference, numerous online platforms offer a wealth of free and paid 3D models. Websites like Thingiverse and MyMiniFactory provide a vast library of user-generated designs, catering to various interests and needs.
For more professional or intricate models, platforms such as TurboSquid and CGTrader offer paid options that guarantee higher quality and exclusivity. Before downloading, check the model’s compatibility with your printer and slicing software. By utilizing these resources, you can quickly find or customize a 3D model that suits your printing projects, saving you time and effort.
Step 3: Prepare the Model for Printing
Slicing Software: What It Is and How to Use It
Slicing software plays a pivotal role in the 3D printing process by converting your digital model into a series of instructions the printer can understand. This software, such as Cura or PrusaSlicer, allows you to set various parameters, including layer height, print speed, and infill percentage. Once the model is loaded, the slicer will generate G-code, which tells the printer how to move its nozzle to create the object layer by layer.
Understanding how to use slicing software is essential for optimizing print quality and reducing material waste. Experimenting with different settings can lead to improved results, helping you achieve your desired outcome effectively.
Setting Print Parameters: Layer Height, Infill, and Supports
Setting the right print parameters is crucial for ensuring a successful 3D print. Layer height, typically ranging from 0.1mm to 0.3mm, determines the print’s resolution and finish quality. A smaller layer height results in finer details but increases print time.
Infill percentage impacts the strength and weight of the printed object; higher infill offers more durability but uses more filament. Additionally, considering supports for overhangs is vital, as they prevent print failures. Balancing these parameters according to your project’s requirements can lead to higher quality prints and improved overall performance of your 3D printer.
Step 4: Choose the Right Material for Your 3D Print
Popular 3D Printing Materials: PLA, ABS, PETG, Resin – Which One to Choose?
Selecting the right material for your 3D print can significantly influence the final product’s quality and functionality. PLA (Polylactic Acid) is a popular choice for beginners due to its ease of use and eco-friendliness; it adheres well to the print bed and produces minimal odor. ABS (Acrylonitrile Butadiene Styrene) is more durable and heat-resistant, making it suitable for functional parts but requires a well-ventilated area due to fumes.
PETG (Polyethylene Terephthalate Glycol) combines the best properties of both, offering strength and flexibility. For high-precision applications, resin printers provide unparalleled detail but can be more complex to use. Understanding the properties of each material will help you select the best fit for your project.
Factors to Consider: Strength, Flexibility, and Print Difficulty
When choosing a material for 3D printing, consider factors such as strength, flexibility, and the complexity of the printing process. For instance, if you’re creating a prototype that requires durability, ABS or PETG might be the better options.
Conversely, if your project requires intricate details and a smooth finish, resin would be ideal. Additionally, some materials are easier to print with than others; beginners may find PLA the most forgiving. Understanding these characteristics will help you make informed decisions that align with the intended use of your 3D printed object, improving the overall success of your project.
Step 5: Set Up and Calibrate Your 3D Printer
How to Properly Calibrate Your 3D Printer to Avoid Print Failures
Calibration is a critical step in the 3D printing process that can make or break your print’s success. Start by ensuring that the printer’s axes are aligned and that the print bed is leveled properly. This involves adjusting the height of the print bed relative to the nozzle, ensuring that there’s just enough distance for the filament to extrude without causing imperfections.
Many modern printers offer automated calibration features, but manual checks are also beneficial. Regular calibration helps maintain print quality and can prevent common printing problems, such as warping and poor adhesion, leading to a more reliable printing experience.
Printer Bed Leveling: Why It’s Critical for Successful Prints
Printer bed leveling is one of the most crucial aspects of 3D printing. An unlevel bed can lead to uneven extrusion and adhesion issues, ultimately resulting in failed prints. To achieve proper leveling, it’s essential to adjust the distance between the nozzle and the print bed at multiple points.
Many printers provide a simple leveling procedure that involves using paper to gauge the gap. Once leveled, the printer will be able to lay down the first layer smoothly, which is vital for the success of the entire print. Taking the time to level your print bed correctly will enhance the reliability of your 3D prints and improve overall quality.
Step 6: Start the Print – Troubleshooting Common Issues
How to Load Filament and Begin Printing
Loading filament into your 3D printer is a straightforward process, but doing it correctly is essential for a successful print. Begin by preheating the nozzle to the appropriate temperature for your chosen filament, whether it’s PLA, ABS, or PETG.
Once heated, insert the filament into the extruder until it reaches the nozzle, ensuring a tight fit. Some printers feature automatic loading mechanisms, while others require manual feeding. After the filament is loaded, start the print job from your slicing software, and monitor the first few layers closely to ensure they adhere properly to the print bed. Proper loading and monitoring will help prevent common printing problems.
What to Do if the Print Fails: Common Problems and How to Fix Them
Print failures can be frustrating, but understanding common issues can help you troubleshoot effectively. One frequent problem is warping, which occurs when the edges of the print lift off the bed. This can often be remedied by using a heated print bed or applying an adhesive like glue stick or hairspray.
Another common issue is stringing, where thin strands of filament are left between parts of the print. Adjusting the retraction settings in your slicing software can help minimize this. Familiarizing yourself with potential printing problems and their solutions will enable you to respond quickly, ensuring a smoother printing experience.
Step 7: Post-Processing – Finishing Your 3D Print
Removing Supports, Sanding, and Smoothing Your 3D Model
Post-processing is an essential step to enhance the appearance and functionality of your 3D print. After the print completes, carefully remove any support structures that were used during the printing process. Depending on the material and the print’s complexity, this can involve cutting away or breaking off supports.
Sanding with fine-grit sandpaper can help eliminate layer lines and imperfections, resulting in a smoother finish. For more advanced techniques, you can apply acetone vapor smoothing for ABS prints or use a heat gun for PLA. Post-processing allows you to achieve a professional look while improving the quality of your 3D printed object.
Painting and Additional Finishing Techniques for Professional Results
Painting your 3D print can significantly enhance its aesthetic appeal and provide a polished look. Before painting, ensure the surface is clean and free of dust or grease, as this will help the paint adhere better.
Priming the print can also create a smoother base for the paint, allowing for more vibrant colors. Use acrylic paints for best results, and consider sealing the painted surface with a clear coat to protect it from scratches. Additional techniques, such as applying decals or using a clear resin finish, can further elevate the appearance of your 3D print. These finishing touches can make a substantial difference, especially for models intended for display.
Conclusion:
3D Printing for Beginners – Final Tips for Success
For beginners venturing into the world of 3D printing, patience and practice are key. Familiarize yourself with your specific printer and its capabilities, and don’t be afraid to experiment with different settings and materials.
Join online communities for support and advice from experienced 3D printing experts. Keep learning about advancements in 3D printing technology, as the field is rapidly evolving. By following the steps outlined in this guide, you will be well on your way to creating impressive 3D models and achieving successful prints.
The Long-Term Benefits of Mastering 3D Printing
Mastering 3D printing can yield numerous long-term benefits, both personally and professionally. As you become proficient in using the technology, you’ll open up opportunities for innovation and creativity in your projects.
The ability to produce custom prototypes can enhance your skills in design and engineering, making you a valuable asset in any industry. Furthermore, understanding 3D printing technology can lead to potential career advancements in fields like product design and manufacturing. Embracing this technology not only enriches your skill set but also positions you to be at the forefront of the future of manufacturing.